
Qué es Chapa metálica ¿Asamblea?
El proceso de ingeniería que consiste en unir dos o más piezas de chapa metálica para formar un producto acabado o un subconjunto se denomina ensamblaje de chapa metálica. Es una fase básica de la producción que viene después de procesos de fabricación de metales como el corte por láser, el plegado y el conformado de chapa. La calidad e idoneidad de los métodos de ensamblaje empleados está directamente relacionada con la integridad, funcionalidad, coste y vida útil de innumerables productos, ya sean las piezas electrónicas de consumo que llevamos en las manos, los vehículos que conducimos o la maquinaria industrial que impulsa nuestro mundo.
La decisión sobre la estrategia de montaje adecuada no es una cuestión menor que pueda tomarse al final de la producción. Es un aspecto de diseño muy importante que tiene consecuencias de largo alcance en el ciclo de vida de un producto. Una buena selección puede reducir significativamente el coste de fabricación, aumentar el ritmo de producción e incrementar la resistencia estructural y la capacidad de servicio. En cambio, una mala decisión puede provocar el fracaso del producto, presupuestos abultados, cuellos de botella en la producción y una mala experiencia del usuario final.
Esta guía ofrece un resumen definitivo de los principales métodos de ensamblaje de chapa metálica. Examinará la mecánica de funcionamiento de cada método, ofrecerá una comparación directa de las capacidades de cada uno de ellos y proporcionará principios de diseño fundamentales para uso de ingenieros, diseñadores y fabricantes de chapa metálica. El objetivo es proporcionarle los conocimientos básicos que necesitará para tomar decisiones informadas y eficaces con respecto a su aplicación concreta, de modo que su producto final no sólo esté unido, sino ensamblado de forma inteligente y robusta.
Técnicas básicas en Chapa metálica Montaje
Los métodos de ensamblaje que pueden utilizarse en la fabricación de chapa metálica son variados y cada uno tiene un perfil distinto de puntos fuertes, puntos débiles y aplicaciones óptimas. Pueden dividirse en procesos térmicos, como la soldadura, procesos mecánicos con elementos de fijación y nuevos métodos de deformación del material o de unión química. El dominio técnico exige comprender todo el espectro de las distintas técnicas.
Soldadura
La soldadura es un método de fabricación que consiste en unir materiales, normalmente metales, fundiendo las piezas y dejándolas enfriar, lo que provoca su fusión. Forma uniones permanentes de alta resistencia que suelen ser más fuertes o iguales que el metal base.
MIG Soldadura
La soldadura por arco metálico con gas (GMAW) o soldadura MIG es un proceso rápido y eficaz que implica un electrodo de alambre consumible alimentado continuamente y un gas de protección para cubrir el baño de soldadura contra la contaminación atmosférica. Es muy flexible y puede utilizarse con muchos tipos de metales, como acero al carbono, acero inoxidable y aluminio. La soldadura MIG es una opción estándar cuando se requiere una producción de gran volumen, o cuando hay que unir secciones más gruesas de chapas planas y la velocidad es un factor importante. Las soldaduras producidas son robustas y pueden necesitar un tratamiento posterior, incluido el amolado, para producir un acabado liso.
Soldadura TIG
La soldadura por arco de gas tungsteno (GTAW) o soldadura TIG es un proceso que emplea un electrodo de tungsteno no consumible para formar el arco y un gas de protección inerte. Normalmente se añade manualmente una varilla de relleno al baño de soldadura. En comparación con MIG, la soldadura TIG es un proceso más lento y preciso. Proporciona un control inigualable, lo que da lugar a soldaduras muy limpias, de alta calidad y estéticamente agradables que a menudo no necesitan ningún tratamiento posterior. Es la forma más popular de procesar materiales de calibre fino (incluidos el aluminio y el acero inoxidable) y cuando el aspecto estético y la precisión son lo más importante, como en la industria aeroespacial, la metalurgia arquitectónica y los bienes de consumo de gama alta.
Soldadura por puntos
La soldadura por puntos de resistencia (RSW) es una técnica rápida de unión de chapas metálicas superpuestas. Funciona haciendo fluir una corriente eléctrica elevada a través de las chapas metálicas mediante dos electrodos de aleación de cobre que sujetan las chapas entre sí. La oposición al flujo de corriente produce un elevado calor localizado que funde el material y fusiona una pequeña pepita fundida entre las chapas. Es muy rápido, no necesita material de relleno y se automatiza fácilmente, por lo que es el proceso de ensamblaje más habitual en la industria del automóvil para montar carrocerías de vehículos en blanco. Su principal inconveniente es que produce uniones localizadas en lugar de una costura.
Soldadura láser
La soldadura por haz láser (LBW) es un método de unión de materiales que utiliza una fuente de calor concentrada, un haz láser de alta densidad. Crea soldaduras estrechas y profundas y una zona afectada por el calor (ZAT) muy pequeña. Esto reduce la distorsión térmica, una ventaja importante cuando se utilizan componentes sensibles al calor o materiales finos. La soldadura láser es muy rápida, precisa y puede aplicarse para unir una gama muy amplia de materiales, incluidos los que son difíciles de soldar con técnicas convencionales. Su adquisición inicial es cara, pero resulta más rápida y de mayor calidad en aplicaciones de precisión de gran volumen.
Soldadura de espárragos
La soldadura de espárragos es un proceso de soldadura por arco especializado y semiautomático que se utiliza para fijar un espárrago roscado, un pasador o una fijación a una pieza metálica. Uno de los electrodos es el propio espárrago. Se trata de un proceso no destructivo que produce una soldadura unilateral de alta resistencia sin dejar marcas en la parte posterior de la pieza. Esto lo hace inestimable en aplicaciones en las que se necesita un acabado exterior limpio, por ejemplo, en cerramientos de equipos, paneles y construcción naval, ya que no requiere taladrado, roscado ni remachado.
Soldadura robotizada frente a soldadura manual
La elección de soldadura robotizada o manual depende del volumen, la complejidad y la repetibilidad. La soldadura manual, realizada por un operario cualificado, ofrece la mayor flexibilidad en trabajos a medida, formas complejas y producción de bajo volumen. Un soldador humano puede ajustarse a las irregularidades y afinar sobre la marcha. En la soldadura robotizada, la soldadura la realizan sistemas automatizados. Ofrece una velocidad, precisión y repetibilidad inigualables en la producción de grandes volúmenes de piezas estandarizadas. Aunque el coste inicial es elevado, los sistemas robotizados ahorran mano de obra, eliminan los errores humanos y proporcionan soldaduras de alta calidad las 24 horas del día.
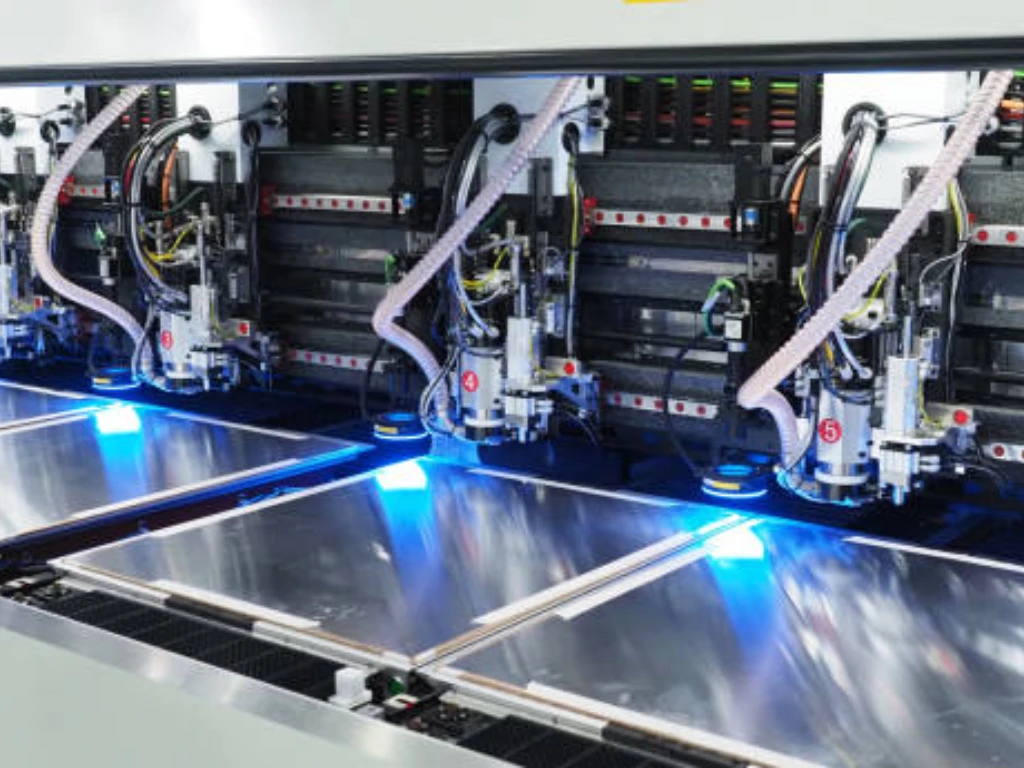
Fijación mecánica
Las fijaciones mecánicas utilizan elementos físicos para sujetar o unir piezas. Suelen ser no térmicas y a menudo fáciles de desmontar, por lo que son necesarias cuando un producto necesita mantenimiento o acceso.
Remachando
El remachado es una forma muy antigua y fiable de fijación mecánica. Un remache es un pasador metálico con una cabeza en un extremo que se inserta a través de orificios en dos o más piezas que están alineadas. El extremo final se deforma con un martillo o una pistola remachadora, formando una segunda cabeza que sujeta permanentemente las piezas entre sí. Una variante común es el remache ciego, o remache pop, que puede instalarse en un lado de la pieza, por lo que es adecuado cuando el acceso es limitado. El remachado ofrece una resistencia superior a la vibración y al cizallamiento.
Fijaciones roscadas
Las fijaciones roscadas son la forma más común de unión mecánica, apreciadas por su resistencia, fiabilidad y facilidad de mantenimiento.
- Tornillos, tuercas y pernos: Con ellos se crean uniones fuertes y sujetas que pueden desmontarse y volverse a montar fácilmente. La selección adecuada depende de la fuerza de sujeción requerida, la compatibilidad del material y la exposición ambiental.
- Insertos: Los insertos roscados se utilizan para proporcionar roscas de máquina duraderas en materiales que son demasiado blandos o finos para soportarlas directamente, como componentes de aluminio o plástico fijados a un armazón de chapa metálica.
- Fijaciones PEM®: Esta categoría de elementos de fijación de cierre automático es la piedra angular del diseño moderno de chapas metálicas. Los elementos de fijación PEM (incluidas tuercas, espárragos y separadores) se introducen a presión en un orificio de tamaño preciso. El material de base fluye en frío hacia una ranura especialmente diseñada en el elemento de fijación, fijándolo permanentemente en la chapa. De este modo, se obtienen roscas fuertes y permanentes en chapas metálicas demasiado finas para roscarlas, lo que revoluciona el montaje de armarios electrónicos, bastidores de servidores y otros dispositivos complejos.
Unión sin remaches (remachado y autoremachado)
El clinchado es un innovador proceso de conformado en frío que une piezas de chapa creando un enclavamiento mecánico localizado. Utiliza un punzón y una matriz para introducir las chapas metálicas en una pequeña hendidura, forzando al material a extenderse hacia fuera y formar una unión duradera de tipo botón. No se necesitan fijaciones ni calor. El proceso es extremadamente rápido, barato y no produce humos ni chispas. Es una opción excelente para unir metales previamente recubiertos o pintados, ya que la superficie protectora no se quema.
Adhesión adhesiva
Los adhesivos industriales contemporáneos, como los epoxis, los acrílicos y los poliuretanos, ofrecen una alternativa eficaz a las técnicas de unión convencionales. La unión adhesiva reparte la tensión uniformemente por toda la superficie unida y elimina las concentraciones de tensión que existen alrededor de las soldaduras o las fijaciones. Esto mejora la resistencia a la fatiga y permite unir materiales distintos, por ejemplo, metal con plástico o materiales compuestos. También forma una unión continua y sellada que puede utilizarse para evitar la corrosión y amortiguar las vibraciones. Una unión eficaz es muy sensible a una cuidadosa preparación de la superficie y al control del proceso de curado.
Formando & Unión integrada
Estos ingeniosos métodos aprovechan la geometría de los propios componentes de la chapa para formar uniones, y eliminan por completo la necesidad de utilizar herrajes separados y, en muchos casos, mejoran la facilidad de montaje. Se trata de ejemplos de conformado de chapa sin necesidad de utilizar un elemento de fijación externo.
Dobladillos y plegados
Un dobladillo es un pliegue realizado a lo largo del borde de una pieza de chapa metálica para formar un borde seguro y liso o para unir dos chapas. En una unión con dobladillo, una chapa se dobla sobre el borde de otra. Esto es típico en la industria del automóvil en paneles de puertas y capós y en la fabricación de electrodomésticos.
Pestaña y Montaje de ranuras
Se trata de una característica de diseño de autolocalización en la que las lengüetas de un lado encajan en las ranuras del otro. Los diseños de lengüeta y ranura garantizan que las piezas encajen perfectamente y luego se suelden o se unan de forma permanente. Esto facilita la fijación, acorta el tiempo de montaje y mejora la precisión dimensional. Las lengüetas pueden doblarse o retorcerse en otras para formar un cierre mecánico semipermanente. Esto también puede ayudar a reducir la necesidad de pestañas redundantes.
Ajuste a presión
Una unión a presión utiliza la flexibilidad del material para crear una conexión entrelazada. Suele incluir un elemento saliente en una pieza (por ejemplo, un gancho en voladizo) que se desvía durante la inserción y vuelve a encajar con un elemento de la otra pieza. Se basa en la fuerza elástica del material. Se trata de un método de ensamblaje extremadamente rápido y económico, ideal para piezas que pueden tener que abrirse para su mantenimiento, como tapas de baterías o paneles de acceso a componentes internos, en función de la frecuencia de uso.
Machihembrado
Al igual que la lengüeta y la ranura, la unión machihembrada consiste en un reborde elevado (lengüeta) en una pieza que encaja en un canal rebajado (ranura) en otra. Esto crea una fuerte costura de enclavamiento que proporciona una excelente alineación y puede añadir una rigidez significativa al conjunto, a menudo utilizado en la construcción de chasis y bastidores.
Elegir el método: Una comparación cara a cara
La selección del método de ensamblaje óptimo requiere un cuidadoso equilibrio entre los requisitos técnicos, las realidades de producción y las limitaciones presupuestarias. La siguiente tabla ofrece una comparación directa de las principales técnicas en función de criterios clave para la toma de decisiones.
Característica | Soldadura (general) | Fijación mecánica | Clinchado (sin remaches) | Adhesión adhesiva | Formación yIntegrado |
Coste | $$ (Trabajo/Energía) | $$ (Hardware) | $ (Sin consumibles) | $$ (Adhesivo/Preparación) | $ (Design-In) |
Fuerza | Excelente (Permanente) | De bueno a excelente | Bien | Bueno (Cizalla) | Regular a buena |
Velocidad de montaje | Medio a muy rápido | Medio | Muy rápido | Lento (tiempo de curado) | Muy rápido |
Materiales aplicables | Acero al carbono, acero inoxidable, aluminio, cobre, aleaciones | Metales, plásticos, compuestos, PCB, madera | Acero dulce, aluminio, aleaciones dúctiles | Metales, plásticos, compuestos, vidrio, caucho | Acero dulce, aluminio, cobre |
Espesor aplicable | 0,5-10 mm (Gama Amplia) | 0,5-12 mm (Gama Amplia) | 0,5-3 mm (Delgado-Medio) | <0,2-10+ mm (Todos) | 0,5-3 mm (Delgado-Medio) |
Equipamiento necesario | Alta (Soldador/Gas/Láser) | Bajo a medio (herramientas/cerrajería) | Medio (Prensa/Herramienta) | Bajo (Dispensador, Horno opcional) | Medio (prensa plegadora/matrices de conformado) |
Desmontaje | No (Destructivo) | Sí (la mayoría de los tipos) | No (Destructivo) | No (Destructivo) | No (Destructivo) |
Estética | De regular a excelente (soldadura TIG, láser) | Regular (Cabezas visibles, a menos que estén ocultas) | Bueno (Apariencia unilateral) | Excelente (línea de unión invisible) | De bueno a excelente (características de diseño integradas) |
Consejos de diseño para Chapa metálica Montaje
Un buen diseño para el montaje (DFA) no es una ocurrencia tardía, es una competencia. Incorporar las cuestiones de montaje en las fases iniciales del diseño supondrá un enorme ahorro en costes, calidad y rendimiento.
- Minimice el número de piezas: El método más sencillo para reducir el coste de montaje es eliminar las operaciones de ensamblaje. Explore si se pueden integrar varios componentes en uno formado más complejo.
- Estandarizar las fijaciones: Siempre que sea posible, utilice el mismo tipo y tamaño de elemento de fijación (tornillos, tuercas, remaches) en todo el conjunto. Así se facilita el inventario, se necesitan menos herramientas y se minimiza la posibilidad de error del operario.
- Utilizar funciones de autolocalización: Diseñe componentes que se autoalineen. Las funciones de lengüeta y ranura, machihembrado y anidado minimizan el uso de fijaciones costosas y complicadas, lo que acelera el montaje y mejora la precisión.
- Garantizar el acceso a las herramientas: Uno de los errores de diseño más frecuentes es colocar un tornillo o una soldadura en un lugar inaccesible para la herramienta necesaria. Imagina siempre cómo se realizará el montaje y asegúrate de que hay suficiente espacio libre para manos, llaves, taladros y cabezales de soldadura.
- Diseño a Montaje Unidireccional: Diseñe el montaje de forma que todas las piezas puedan añadirse en una dirección, normalmente de arriba abajo. Esto facilita el montaje manual y robotizado, y no es necesario girar y reorientar la pieza.
- Piensa en las tolerancias: Conozca cómo se acumularán las tolerancias dimensionales de las piezas individuales en el conjunto final. Un análisis inadecuado de las tolerancias puede dar lugar a piezas mal ajustadas. Asegúrese de que los tamaños de los orificios se especifican correctamente para el elemento de fijación seleccionado, especialmente los elementos de fijación a presión, como los elementos de fijación PEM.
Selección de materiales para Chapa metálica Montaje
La elección del material de la chapa influye fundamentalmente en la elección del método de montaje.
- Acero al carbono: Es el caballo de batalla de la industria. Es resistente, barato y fácilmente soldable con casi cualquier técnica. Es un candidato excelente para todos los tipos de fijación mecánica y conformado. Su principal desventaja es su susceptibilidad a la corrosión si no se recubre o pinta adecuadamente.
- Acero inoxidable: Valorado por su resistencia a la corrosión y su atractivo estético, el acero inoxidable puede unirse mediante la mayoría de los métodos. Sin embargo, es más difícil de soldar que el acero al carbono, y a menudo requiere la precisión de la soldadura TIG para mantener sus propiedades y su aspecto. También es más duro y puede provocar un mayor desgaste de las herramientas durante las operaciones de fijación mecánica.
- Aluminio: Ligero y resistente a la corrosión, el aluminio es fundamental para las industrias aeroespacial y del automóvil. Su elevada conductividad térmica y su capa protectora de óxido hacen que la soldadura sea más compleja, por lo que suele requerir procesos especializados TIG o MIG de corriente alterna. Es un material blando, por lo que hay que tener cuidado de no dañar las roscas; se recomienda encarecidamente el uso de insertos roscados o tornillería autoblocante.
Evitar lo común Chapa metálica Peligros del montaje
Conocer los modos de fallo habituales es el primer paso para prevenirlos.
Error: Soldadura Distorsión (Warpage): El calor intenso y localizado de la soldadura provoca dilataciones y contracciones desiguales, que pueden deformar materiales finos.
- Prevención: Utilice fijaciones robustas para sujetar las piezas de forma segura durante la soldadura y el enfriamiento. Utilice una secuencia planificada de soldaduras cortas (soldadura por puntos) en lugar de una soldadura larga y continua. Utilice el menor aporte térmico posible para una fusión adecuada y considere un proceso de baja distorsión como la soldadura láser.
Error: Preparación incorrecta de los orificios para las fijaciones: Los orificios demasiado grandes o demasiado pequeños para las fijaciones o remaches de cierre automático darán lugar a una unión débil que fallará bajo carga.
- Prevención: Cumpla estrictamente las especificaciones del fabricante del elemento de fijación en cuanto al tamaño del orificio, las tolerancias y la distancia mínima desde un borde. Utilice punzones y matrices afilados y de alta calidad para crear orificios limpios y precisos.
Pitfall: Sujetador Stripping o Pull-Through: Apretar demasiado un tornillo en un material fino o blando puede dañar las roscas o hacer que la cabeza del tornillo atraviese la chapa.
- Prevención: Utilice destornilladores de par controlado para aplicar la cantidad correcta de fuerza. Aumente la superficie de apoyo bajo la cabeza del tornillo utilizando una arandela. Para uniones críticas, especifique el uso de tuercas autoblocantes más resistentes en lugar de orificios roscados.
Error: Fallo de la unión adhesiva: Una junta adhesiva falla debido a una mala preparación de la superficie, lo que provoca delaminación.
- Prevención: Siga un protocolo estricto de limpieza y abrasión de la superficie para eliminar todos los aceites, suciedad y óxidos. Asegúrese de elegir el adhesivo adecuado para los sustratos y de aplicarlo y curarlo siguiendo las instrucciones precisas del fabricante en cuanto a temperatura y tiempo.
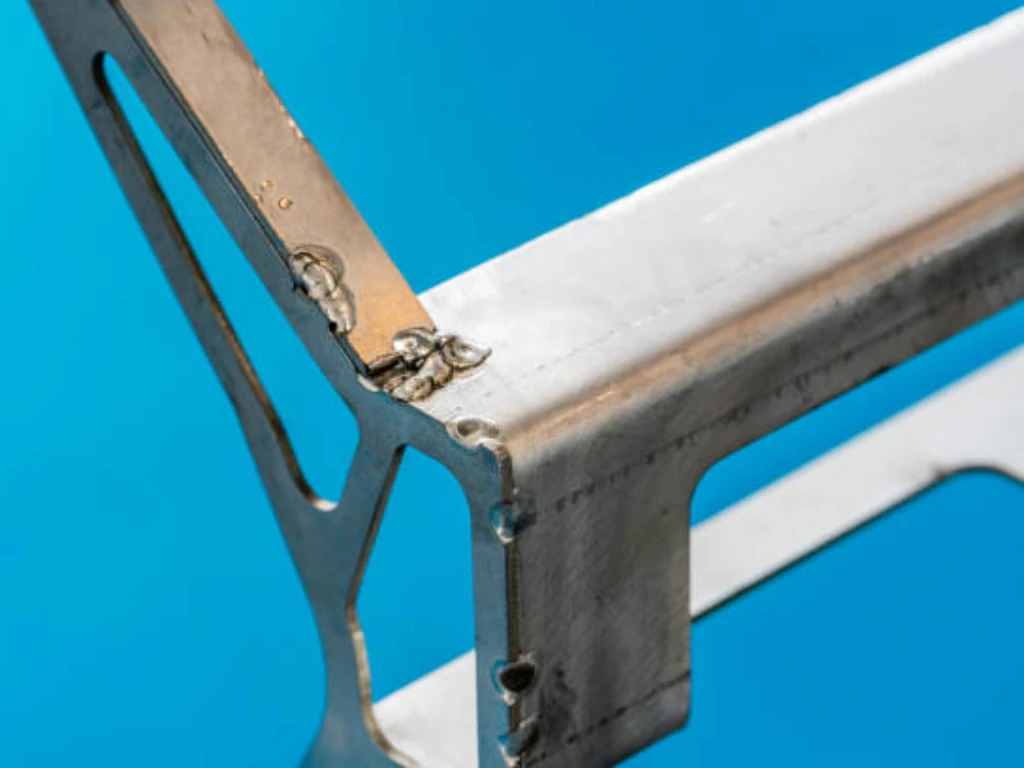
Tendencias futuras y su próximo proyecto
El campo del ensamblaje de chapas metálicas evoluciona continuamente. Estamos asistiendo a un aumento de las técnicas híbridas, como la "unión por soldadura", que combina la soldadura por puntos con adhesivos para crear uniones rígidas y muy resistentes a la fatiga. Los avances en la tecnología láser de fibra hacen más accesible la soldadura de alta velocidad y baja distorsión. En la búsqueda del aligeramiento, sobre todo en el sector de los vehículos eléctricos, la unión adhesiva y la fijación mecánica avanzada están sustituyendo a la soldadura tradicional para unir la compleja mezcla de aceros de alta resistencia, aluminio y materiales compuestos.
Sin embargo, los principios fundamentales permanecen constantes. Un montaje de éxito nace de un profundo conocimiento de las técnicas básicas, un enfoque disciplinado del diseño y una relación de colaboración entre diseñadores y fabricantes. Cuando se embarque en su próximo proyecto, utilice esta guía como base. Analice las ventajas y desventajas, diseñe con intención, tenga en cuenta los plazos de entrega de los distintos métodos y las implicaciones del grosor del material y el acabado superficial deseado, como el recubrimiento en polvo, y elija el método que ofrezca el equilibrio óptimo de rendimiento, calidad y coste para su aplicación única.
Asóciese con TZR: Su experto en ensamblaje de chapa metálica de precisión
Comprender la teoría del ensamblaje de chapas metálicas es el primer paso. Para salvar la distancia entre la teoría del diseño y la producción impecable hace falta algo más que equipos: hace falta un verdadero socio de fabricación. En TZR, convertimos ideas complejas de chapa metálica en componentes de alta precisión listos para la producción y construidos para su éxito.
Trabajamos en todas las fases del ciclo de vida del producto, desde la consulta inicial de diseño hasta el montaje a gran escala, para sectores en los que el rendimiento no es negociable, como la automoción, los dispositivos médicos, la impresión 3D y las energías renovables. Nuestra amplia experiencia con el acero, el acero inoxidable, el aluminio y el cobre nos permite optimizar cada material en cuanto a resistencia, conformabilidad y rentabilidad.
No sólo cumplimos las normas del sector, sino que las superamos. Con un rendimiento de primera pasada 98% y procesos de calidad de nivel ISO, puede confiar en cada pieza que le entregamos. Nuestro enfoque colaborativo incluye revisiones gratuitas del diseño para fabricación (DFM) y presupuestos rápidos y precisos en menos de dos horas, lo que le ayuda a reducir riesgos y acelerar los plazos.
Cuando la precisión importa y la velocidad es fundamental, asóciese con TZR. Hagamos realidad su próximo diseño con claridad, confianza y una artesanía inigualable.